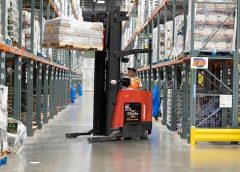
State-of-the-art tech tools help keep the beverages flowing
[ad_1]
For nearly a century, Odom Corp. has distributed beverages across the Pacific Northwest, serving customers ranging from stadium venues and grocery stores to restaurants and mom-and-pop diners. Founded in Alaska in 1932, the company has since expanded into Washington, Oregon, Idaho, and Hawaii. Today, the Bellevue, Washington-based company delivers more than 30 million cases of beer, wine, cider, and soda per year.
It accomplishes all that with 1,650 employees working in four distribution centers that occupy more than 700,000 square feet of space. But as the company added new suppliers, locations, and stock-keeping units (SKUs) over the years, it found it increasingly difficult to standardize operations and monitor end-to-end performance across the enterprise.
After evaluating the operation, company leaders drew up a “wish list” of what they wanted in a solution: They needed a way to provide a standardized operator experience across the company as well as gain better visibility into picking, labor, and costs. And because labor challenges are prevalent in the industry, they also needed a uniform way to train and retrain operators across multiple pieces of equipment throughout the four-state operation. And finally, they needed a technology solution to tie it all together—one that would allow them to track activity and communicate across the entire enterprise to ensure customers receive the correct shipment on the promised date.
STANDARD PROCEDURES
For help finding a solution, Odom turned to lift truck manufacturer and logistics technology vendor The Raymond Corp. in 2014. Initially, Odom was interested mainly in Raymond’s iWarehouse Intelligent Warehouse Solutions suite, which includes a fleet and asset management system and a labor management system (LMS). But as the years passed, it became more firmly entrenched in the Raymond ecosystem. By 2021, Raymond was providing Odom with complete intralogistics solutions composed of telematics and other software systems, operator-assist technologies, more than 100 lift truck models, racking, energy solutions, maintenance agreements, tracking, and more.
A key advantage of this arrangement is that all of those tools operate as a single, integrated set of solutions that provides a comprehensive view of the company’s entire enterprise, Odom says.
“Instead of having 10 to 15 different brands of equipment in the warehouse, we had one holistic experience, all connected with one integrated technology solution. That really gave us a lot of advantages,” Mike McCartney, director of operations, the Odom Corp.–Alaska, said in a prepared statement.
For instance, with one brand of product, operators know what to expect when they get on a piece of equipment. The standardization of equipment across Odom’s facilities also means that an employee from one site can go help out at another without requiring any additional training, which reduces labor costs.
Similarly, the integrated technology bundle has allowed Odom to gather information on its fleet, assets, and workforce throughout the enterprise—information it can then use to enhance efficiency and reliability. For instance, the iWarehouse suite’s LMS provides Odom with clear visibility into where and how labor dollars are being spent, allowing the distributor to quickly and easily analyze costs and identify inefficiencies—such as missing time—at every level of the operation. In fact, since initial implementation, Odom has seen an 86% drop in missing or unaccounted-for time—down to 36%.
A WELCOME ASSIST
At the same time, the operation’s accuracy has improved, thanks to an operator-assist system that has helped Odom address one of its biggest weaknesses: operators putting cases on the wrong pallet. The technology in this case is the Raymond Pick2Pallet product, a put-to-light technology within the truck forks that’s designed to reduce picking errors. Odom’s system, which was custom engineered for use with beverage pallets, uses a combination of colored LED lights and audible instructions to provide directions and reinforce correct product placement.
The Raymond Pick2Pallet system not only allowed Odom to train and develop its pickers quickly, but also allows supervisors to take swift corrective action if they see problems developing.
“When we see the employees’ errors increasing, we will put them on the “Pick2Pallet LED Light System” jacks, and within a single day, their errors are reduced to an acceptable level,” Odom’s Vaughn Sommerseth, warehouse manager, NW Beverages, said in the statement.
Together, the equipment and suite of logistics technologies are helping Odom reduce errors, cut costs, and boost productivity, supporting a consistent experience across all of its locations as the company continues to grow.
[ad_2]
Source link